Reliability and Performance
A proposal designed to assist you in the preventive identification of any latent weaknesses in the product that may risk developing into failures and field returns.
The increasing complexity of electronic products is certainly a major challenge for production lines, given that their evolution is not as fast or immediate. In order to facilitate the electronic manufacturing chain, within the framework of product industrialization, PreventLab has developed an analytical proposal capable of providing comprehensive reporting on the reliability of the device (assembled board) before its introduction to the market.
Starting from an analysis plan during the prototyping phase, it will be possible to validate the quality level of your work and potentially implement improvements in a virtuous process to achieve the success of the finished product.
The method
For a more comprehensive validation plan, PreventLab's proposal consists of multiple analytical solutions accompanied by essential tests in climatic or Shock chambers to proactively identify any latent issues or weak points.
In technical terms: Highly Accelerated Life Test (HALT), not to be confused with: Highly Accelerated Stress Screens (HASS), also known as 'Burn-in', tests specifically designed to eliminate the so-called 'weak population', which includes all components or boards that are prone to 'infant mortality'.
The "bathtub" graph, used to represent the life of a product, shows how, through accelerated aging, data is obtained to characterize the area with a Constant Failure Rate, the operating area where the product has the lowest probability of failure.
The Validation Plan
A Tried and Tested Method
INITIAL CONDITION VERIFICATION
Evaluation of the overall condition of the electronic assembly at time zero: visual inspection performed by certified IPC personnel (CIS),X-ray analysis of solder joints, and assessment of process cleanliness level. For a more detailed verification,metallographic cross-sectioning can be performed to identify any micrometric defects in the joint or laminate.
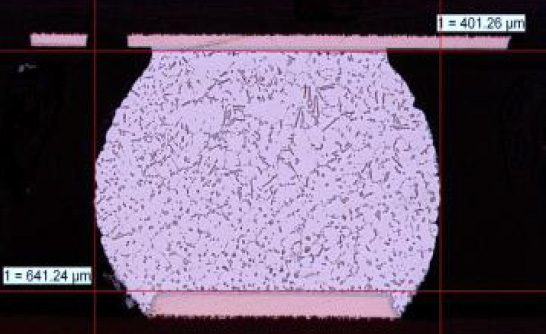
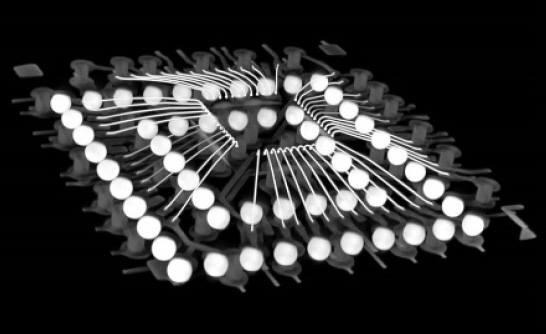
ACCELERATED AGING
The electronic assembly is subjected to simulated aging in a climatic chamber and/or thermal shock, using standard cycles typically with a thermal excursion of 100°C. Through this process, within a few weeks, it is possible to verify the product's durability as if it had been in service for years.
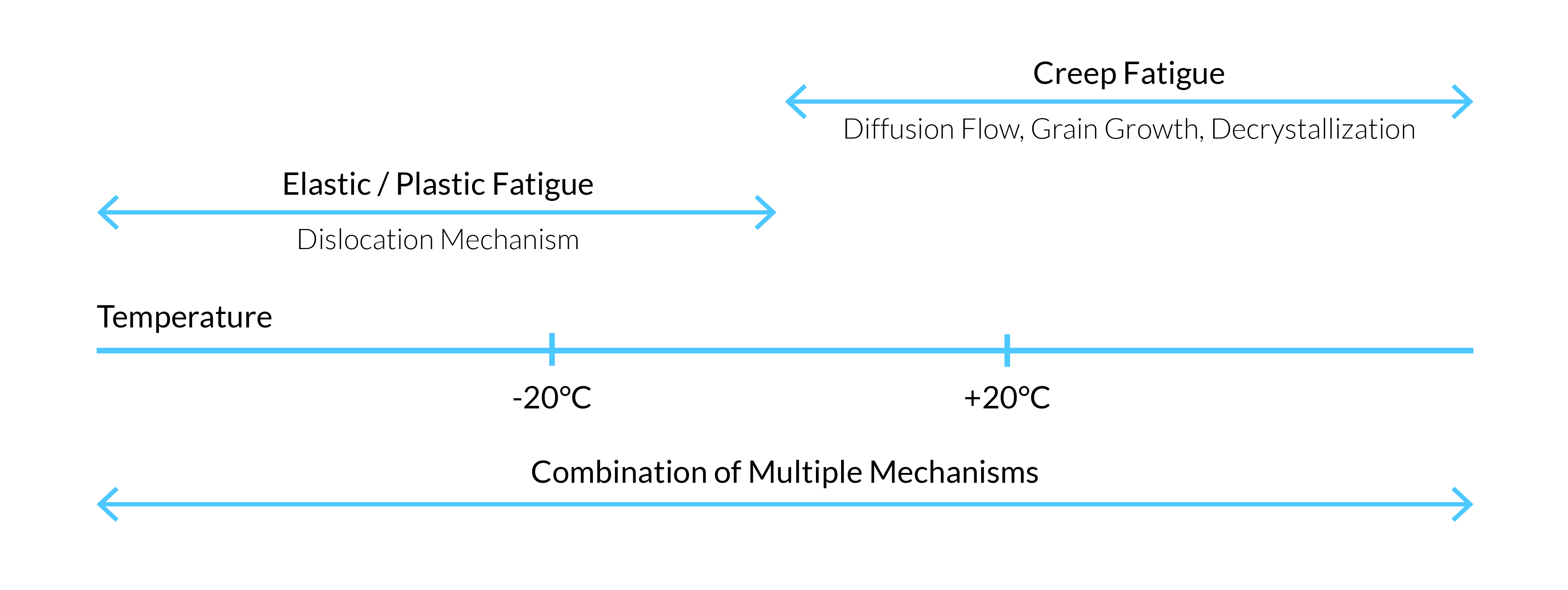
3. FINAL CONDITION VERIFICATION
After the accelerated aging tests, it is necessary to repeat the evaluations performed at time zero to examine the emergence of any defects such as micro-cracks or detachment of metallographic joints, as well as the condition of the laminate and the entire printed circuit (PCB). Additional support for targeted verification of the degradation of some components is provided by the electrical test or ICT (In Circuit Test).
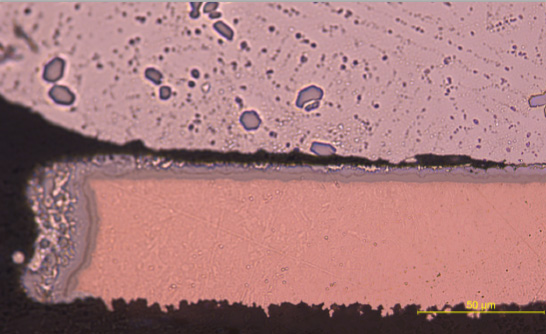
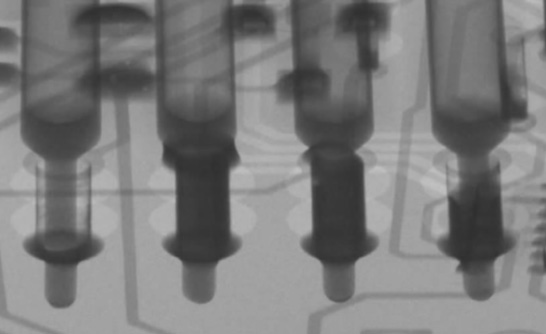
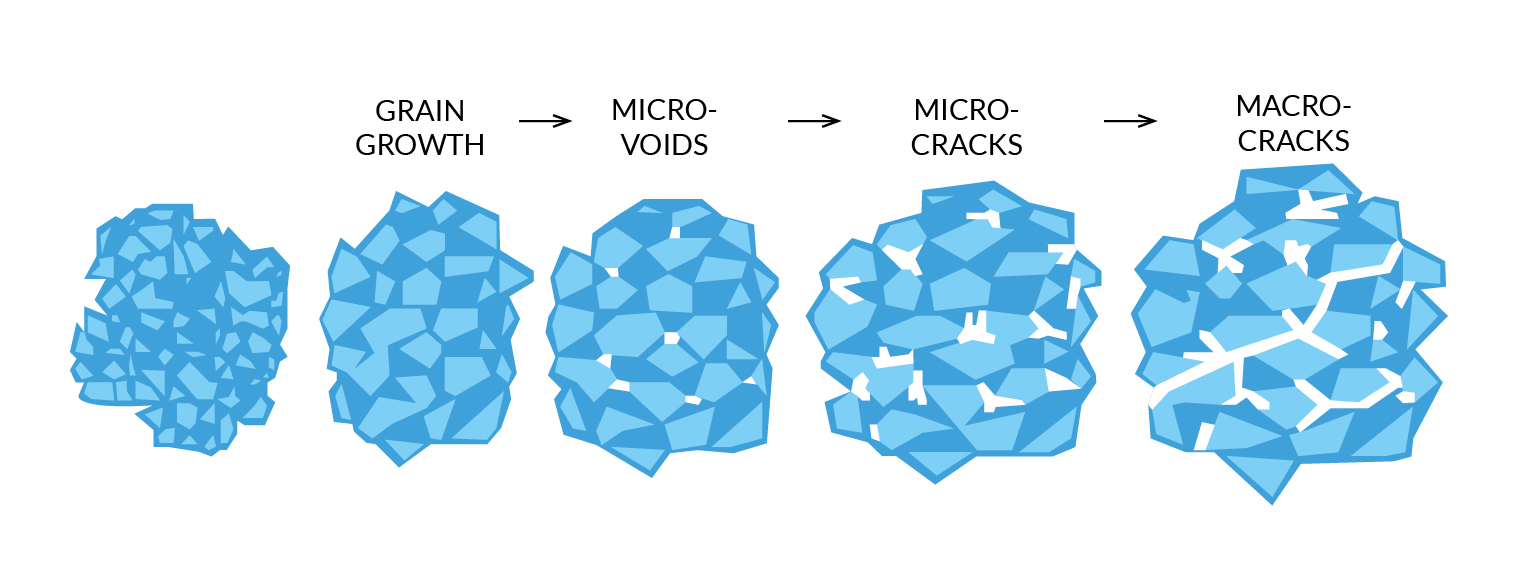
START NOW!
Fill out the form and you will be contacted for any information and quotation related to the service.
FAQ - Product and Process Qualification
Thanks to accelerated aging tests, it's possible to verify the reliability and durability of a product in a reduced timeframe, highlighting any otherwise undetectable issues that could manifest in the field and lead to significant economic and reputational damages.
The test parameters are agreed upon with the customer based on the product specifications and their needs. We leverage our years of experience to provide an optimal solution, always compliant with current regulations for each relevant sector.
The total maximum payload capacity is 100 kilograms: 4 kilograms if the products are loaded on a grated shelf, 50 kilograms in the case of trays, which are more resistant.
Yes, in the case of thermal shock chambers, at least 4 meters of cable are required, while in the case of climatic chambers, the length is reduced to 2 meters.
The limit is only related to the size of the items inserted: this concerns both the horizontal surface (75x31 centimeters per shelf/tray) and the height, which beyond 5 centimeters can affect the number of shelves/trays that can be inserted into the chamber.
Is there a limit to the number of samples that can be placed in the climatic chamber simultaneously?
In this case as well, the limit is related to the size of the items inserted, considering that the internal volume of the chambers is significantly larger compared to the thermal shock chambers.
Yes, all the chambers we have are certified for Industry 4.0: they are remotely connected and communicate with a single management software that records the test parameters.