CONFORMAL COATING, WHICH TYPE AND HOW TO APPLY
It is advisable to wash the boards before proceeding with the coating process, as some fluxes, although no-clean, leave residues that can worsen adhesion and lead to the eventual detachment of the protective coating over time.
The cleanliness of the board's surface also affects its surface tension, which in turn influences the wetting of the PCB by the resin.
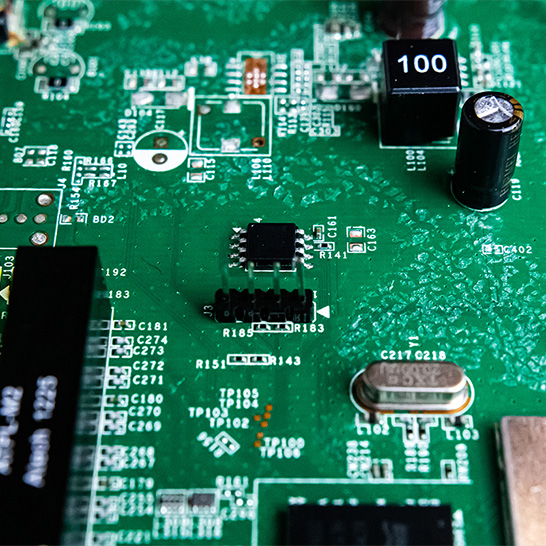
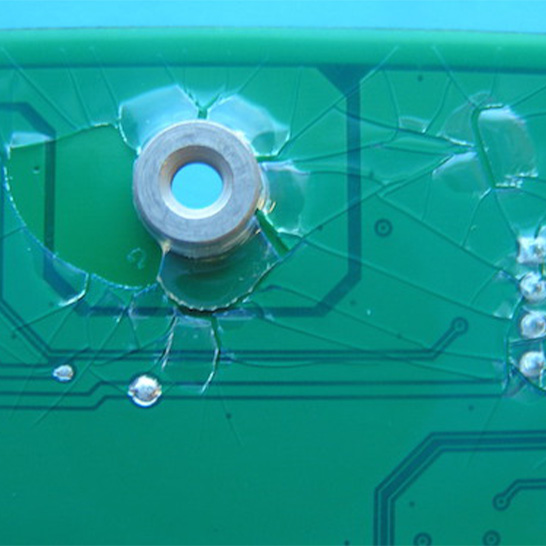
Working in prevention
It is advisable to wash the boards before proceeding with the coating process, because some fluxes, although no-clean, leave residues that, worsening the adhesion, cause the protective coating to peel off over time.
The cleanliness of the board surface also affects its surface tension, which in turn affects the wettability of the PCB by the resin.
Qualification Procedure
There are primarily two reference standards for defining a validation process for protective coatings: IPC-CC-830 and IEC 61086. Below is a brief list of analyses and considerations to address when introducing protective coatings to your electronic products.
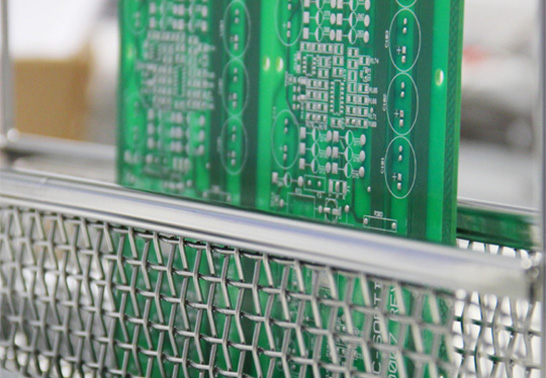
Ionic Contamination
& Dyne Test
To apply conformal coating uniformly and effectively, it is essential to know the cleanliness level of the board and to verify the surface or solder mask's surface tension using specific markers or liquids.
Both the Ionic Contamination Test (TIC) and the dyne test provide results in just a few minutes, allowing for corrective actions, such as washing the boards, before proceeding with the application of the coating. Understanding the cleanliness level of the board adds an extra layer of assurance to prevent future failures due to contaminants trapped beneath the protective coating.
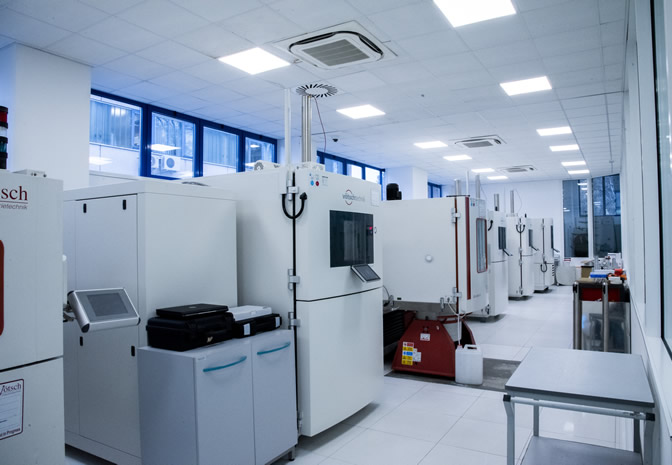
Environmental Tests
Both the IPC-CC-830 and IEC-61086-2 standards include tests with thermal cycles or shock ,to be conducted after the coating has cured, in order to verify the integrity of the structure under various field conditions.
Additionally, humidity or heat-humidity tests (damp heat tests) are performed to assess the hydrolytic stability of the coating, meaning its ability to remain chemically stable when exposed to high levels of humidity and temperature over an extended period. Finally, for naval applications or installations in marine environments, it is advisable to conduct corrosion tests using salt spray .
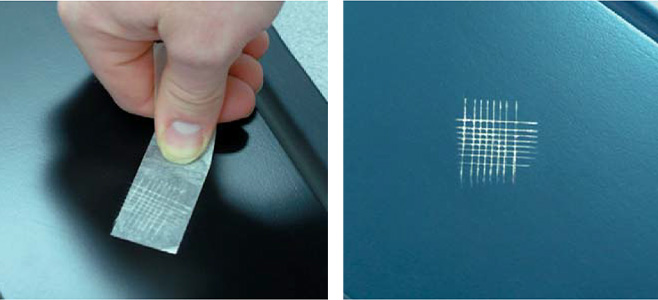
Adhesion and Thickness
Don't overlook the resistance of the coating to detachment from the surface of the board with simple adhesion tests. Depending on the type of paint—acrylic, silicone, etc.—the thickness of the applied product will also vary.
This parameter can be controlled using various techniques: micrometer, metallographic sectioning, special optics capable of calculating the material thickness by knowing its refractive index, etc. This is crucial to avoid excessive stress on the electronic board or uneven deposition that would impair the protective capability of the coating.
START NOW!
Fill out the form and you will be contacted for any information and quotation related to the service.